Production
What we produce, works. Even after the millionth cycle.
Injection molding that fits your part
Our fully automated production is tailored to use the right process for your component – based on geometry, material, and series size.
Together with you, we define the most technically and economically efficient solution.
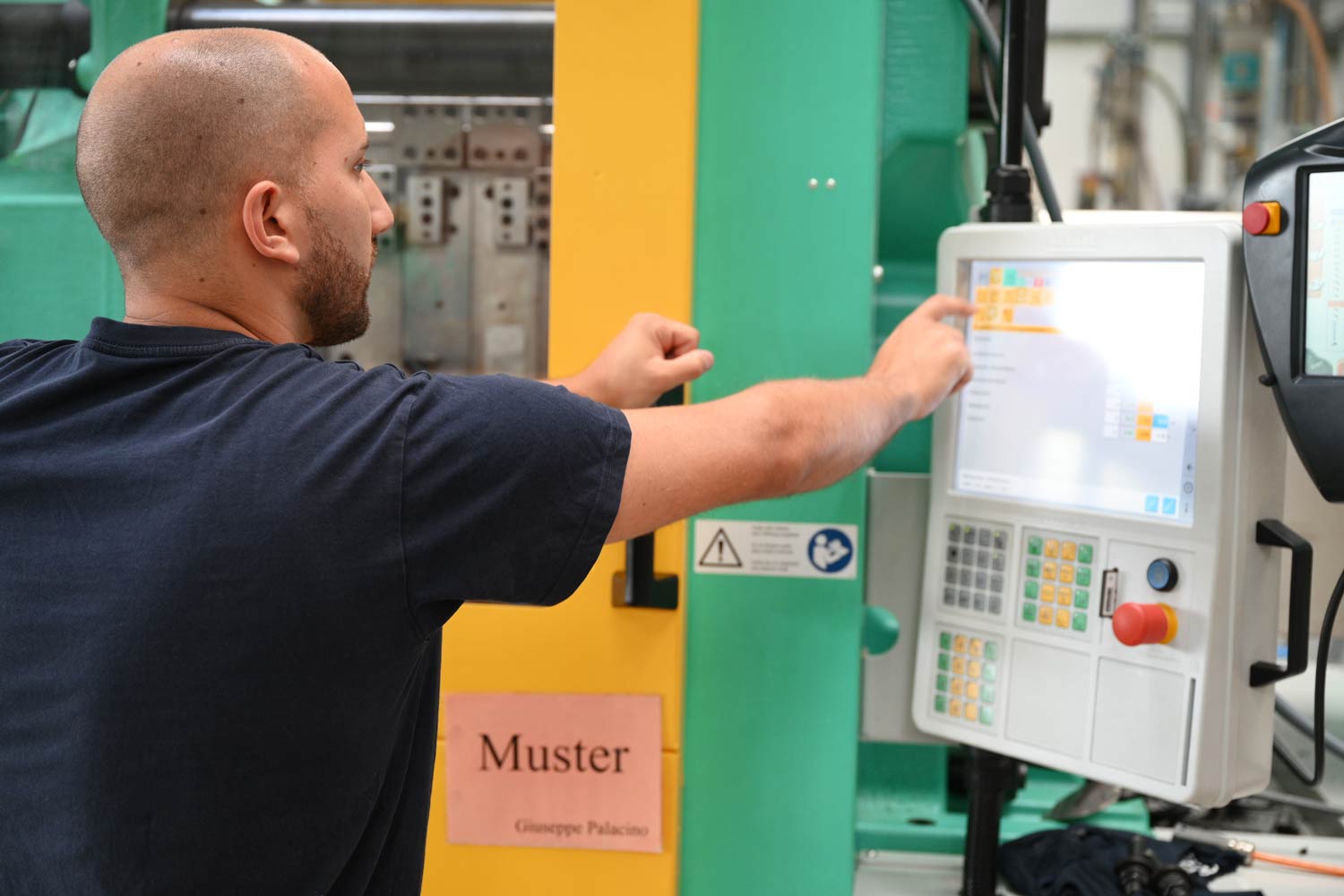
What sets us apart from other molders
We often encounter three topics: high-volume production, metal substitution, and fluid-handling systems. And that’s exactly where our capabilities shine:
Specialty
High-Volume Series
With over 65 injection moulding machines, 24/7 operation and in-house tool expertise, we are designed for high volumes. Series processes are automated, monitored and documented. Two independent production sites also ensure security of supply.
Our series production guarantees:
Specialty
Metal Substitution
Want to reduce weight, cut costs, or simplify assembly? Our expertise in metal substitution delivers.
We replace metal parts with high-performance plastics – without compromising function, sealing, or stability.
From material selection and design adjustments to production-ready solutions, we support every step.
Key benefits:
Specialty
Fluid-Carrying Systems
When plastic parts need to seal, channel, or deliver – even under pressure – design alone isn’t enough.
We have years of experience in fluid-handling parts for air, water, and more. From initial design to series production, function and quality come first.
We focus on what’s critical: Precise wall thickness, homogeneous surfaces, reliable sealing geometries, efficient demolding
Materials that go the extra mile
We process polymers designed to handle extreme demands:
High temperatures, aggressive media, tight tolerances, mechanical loads.
Even plastics with 50% glass fiber content are part of our daily operations.
Technical standard plastics
PA6, PA6.6, PA12, POM, PC, PBT, PETP, PPE+SB
Special types & modified grades
PA 4.6, PA-X, PA6-3-T, PUR
High-performance plastics
PEEK, PPA, PSU
On request
Custom coloring, recycled materials, or specialized compounds
Two sites – one standard
With Eppingen and Bohmte, we operate two powerful production sites – each with their own machine fleet, QA system, and proven workflows.
This decentralized setup boosts both our flexibility and capacity – ensuring reliable supply even when conditions shift unexpectedly.
Real-time quality, not just control
Production means nothing without function.
That’s why our shopfloor management keeps production and QA teams closely aligned – right at the part, not just behind the screen.
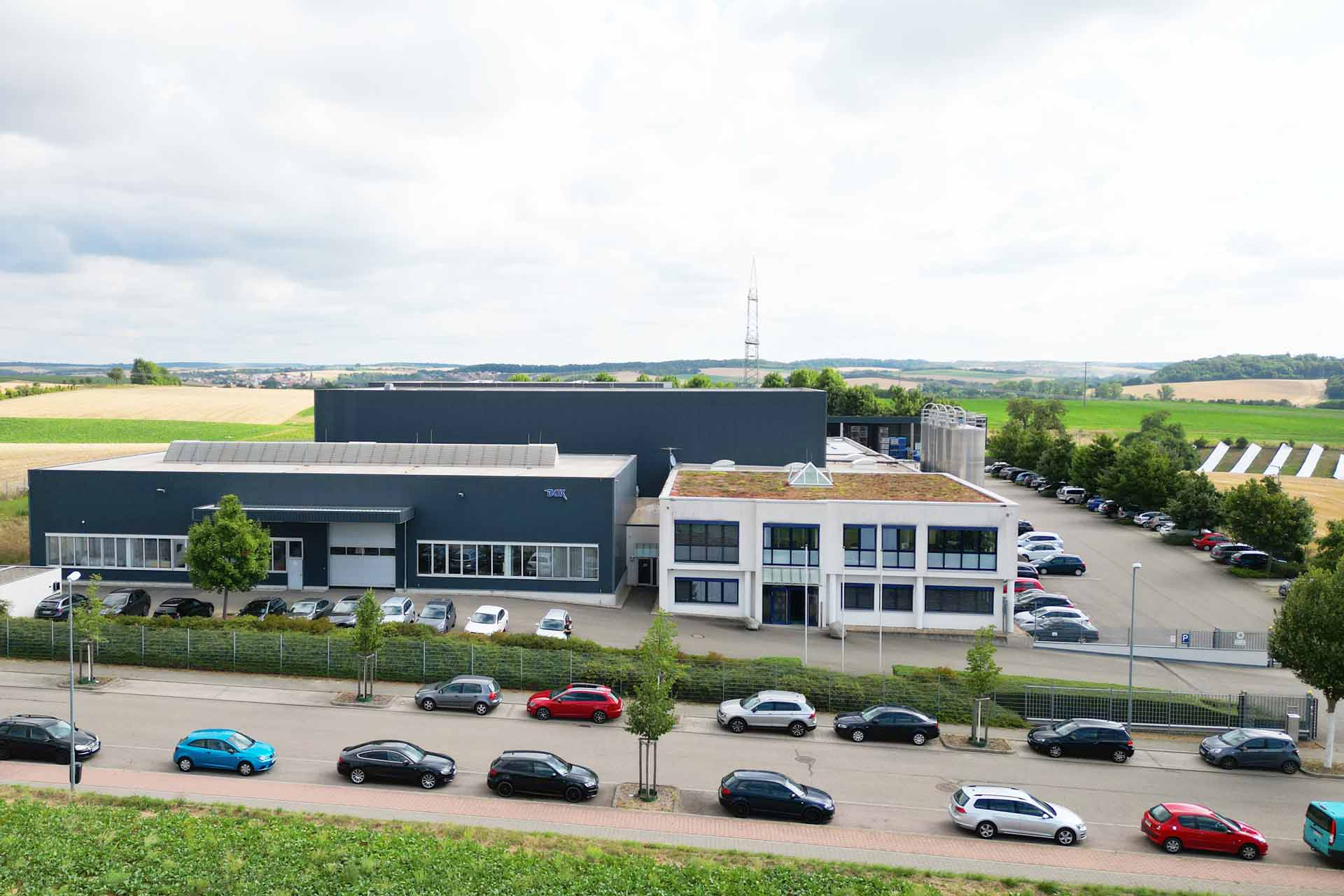
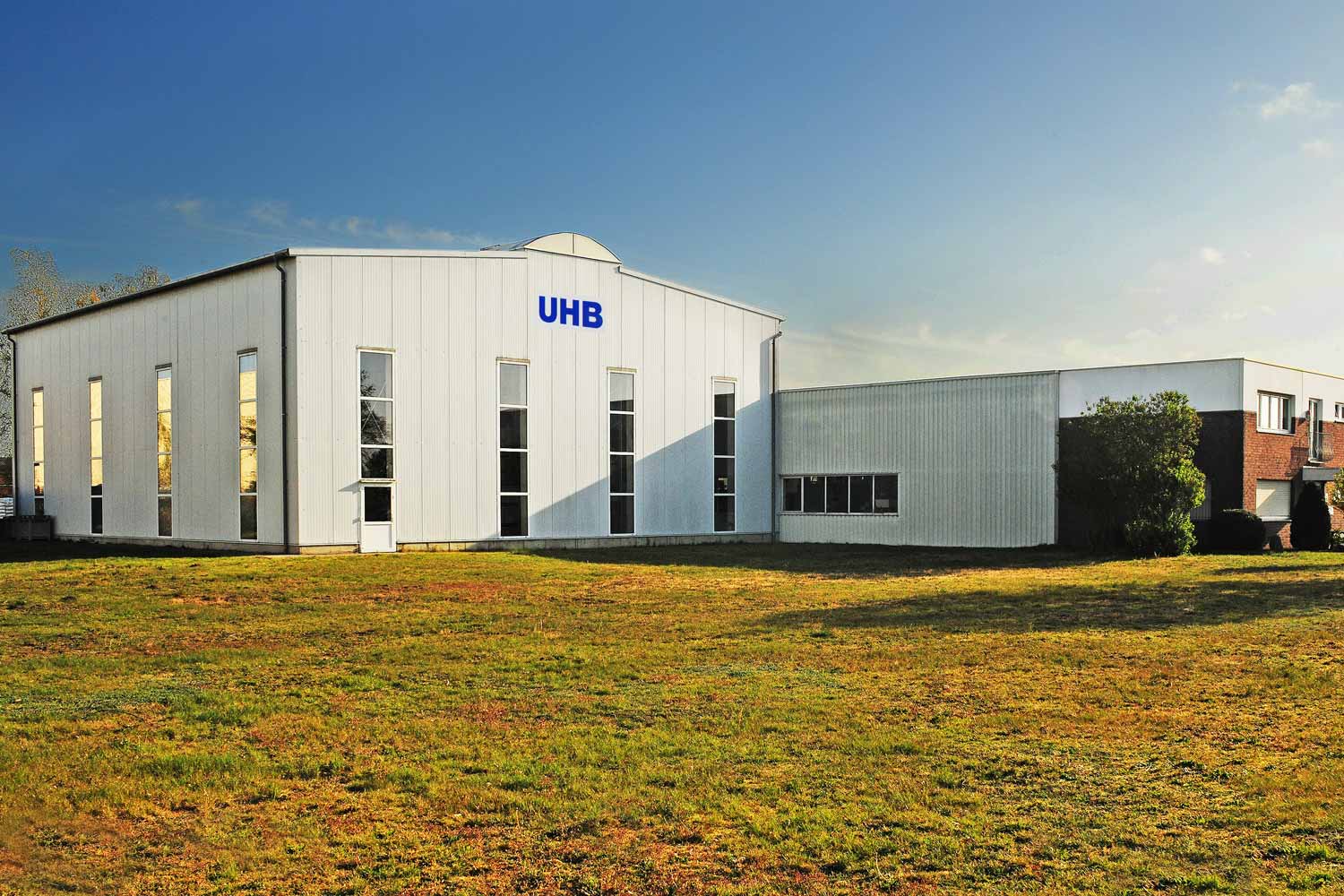
Production through to the functional component
We not only manufacture your plastic parts, we also finalise them until they are fully functional. Our production also incorporates additional processing steps, such as the integration of inserts or customised colouring. This results in components that are ready for use from the very first cycle.
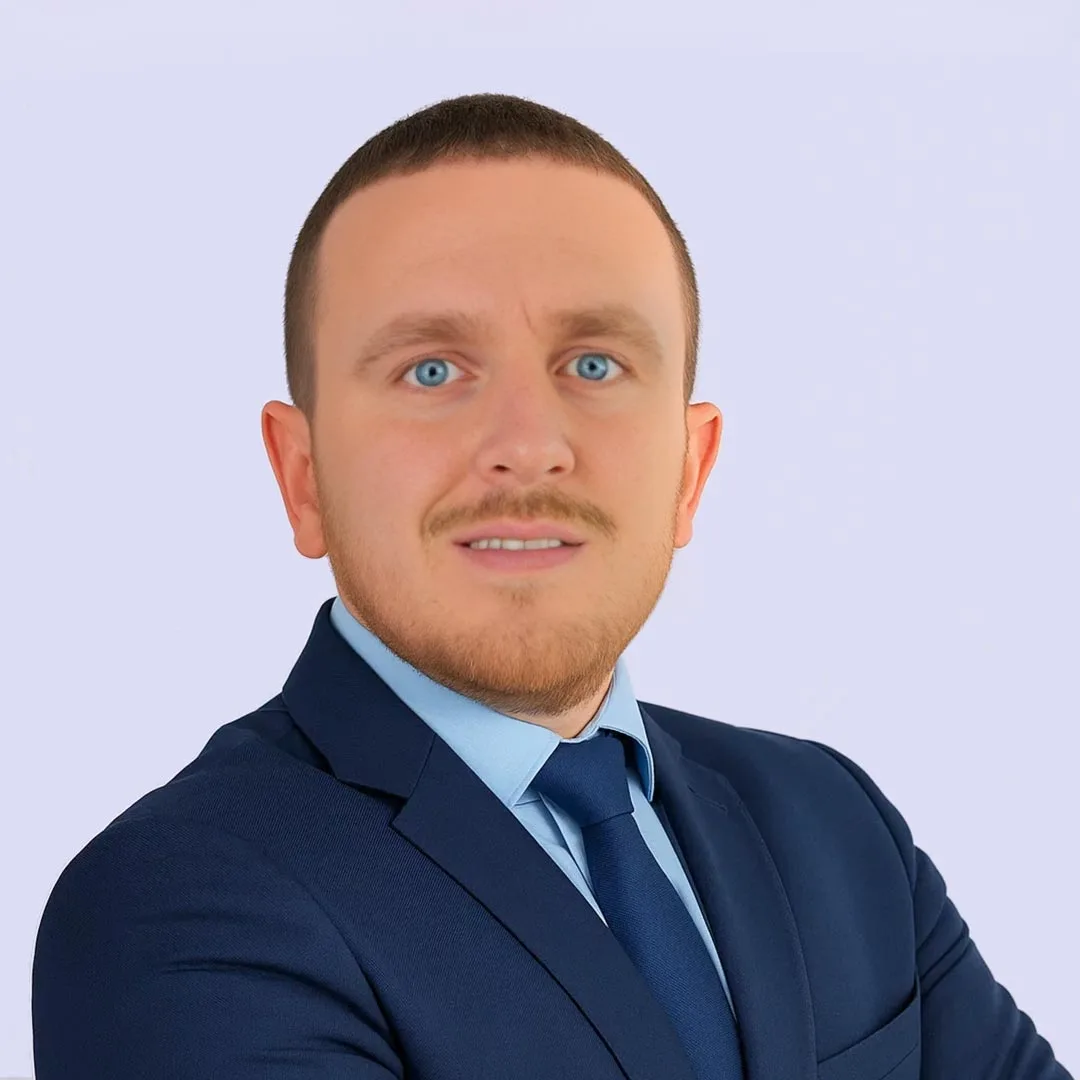
Dimitri Adam
Technical Sales
Ready for stable series processes?
What challenge can we solve for you?
Make a production inquiry now.